Ziel des durch das BMBF geförderten Projektes H2-Digital war die Schaffung einer Simulationsplattform zur Bewertung des Einsatzes von Wasserstoff als zusätzlichen Energieträger zur Eigenstromerzeugung in Fabriken. Dazu wurde eine Co-Simulation von Energiequellen, -senken, -speichern und -wandlern entwickelt. Mit dieser kann die gesamte Prozesskette von der Energieerzeugung bis zu den Verbrauchern virtuell abgebildet werden. Für die energetische Auslegung und den verbrauchsoptimierten Betrieb der im System beteiligten Komponenten war eine möglichst genaue Kenntnis der Energieverbräuche notwendig. Bestehende Ansätze zur Simulation des Energieverbrauchs basieren auf der Annahme konstanter Energieverbräuche für definierte Maschinenzustände oder weisen eine geringe zeitliche Auflösung von mehreren Minuten auf. Ziel war es daher, den Energieverbrauch hochaufgelöst für die jeweilige Bewegung einer Maschine bzw. Anlage bestimmen zu können. Anhand eines demonstrativen Anwendungsfalls wird eine Simulationsumgebung auf Maschinenebene präsentiert. Mit Hilfe dieser Umgebung ist die Vorhersage des applikationsspezifischen Energieverbrauchs auf der Basis einer Bearbeitungsaufgabe möglich.
Erstellung physikalisches Modell Roboter
Das Zusammenspiel mehrerer Maschinen, unterschiedlicher Fertigungsprozesse und deren zeitliche Taktung kann im Rahmen einer Fabriksimulation (vgl. Abb. 3) untersucht werden. Innerhalb des Projektes H2-Digital wurde dazu mit der Abteilung für Fabriksystemdesign und Produktionsplanung zusammengearbeitet. Die Koordination der zeitlichen Abfolge der Einzelprozesse erlaubt es beispielsweise Lastspitzen zu glätten, die direkten Einfluss auf die Energiekosten eines Unternehmens haben. In Kombination mit Modellen zur Erzeugung erneuerbarer Energie und Batteriespeichern lassen sich verschiedene Stromversorgungsstrategien untersuchen und optimierte Betriebspunkte finden.
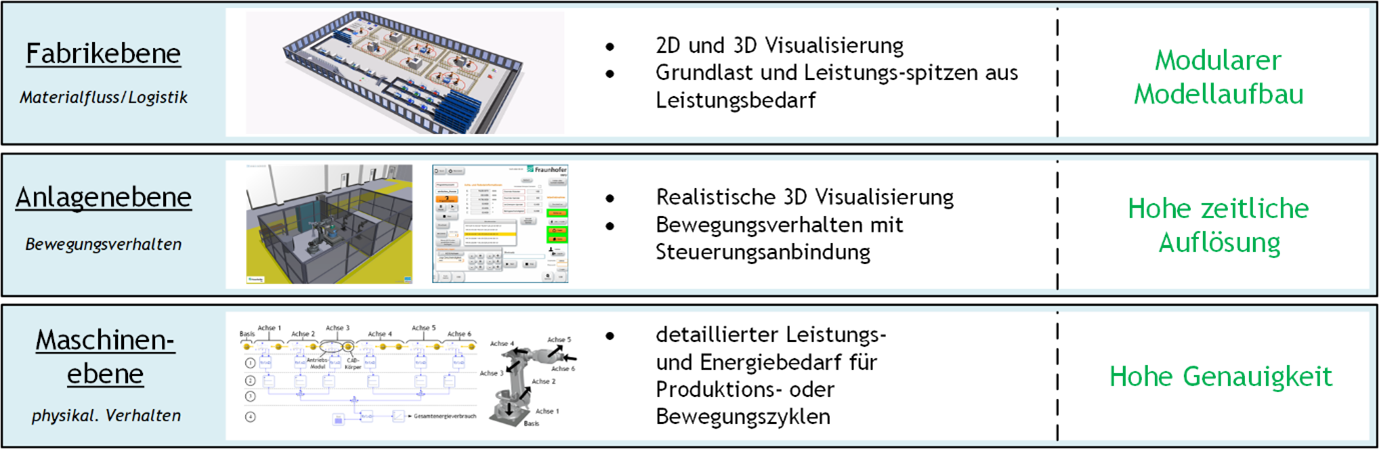
Dafür ist es notwendig den Energieverbrauch auf Anlagen- und Maschinenebene genau zu kennen und vorhersagen zu können.
Da Roboter vielfältig in der Industrie eingesetzt werden und deren Verbreitung stetig zunimmt, wurde als Anwendungsbeispiel ein 6-Achs Roboter der Firma Comau gewählt. Dieser wurde dann zunächst auf Maschinenebene mit der für die Vorhersage des Energieverbrauchs notwendigen Detailtiefe modelliert. Für die Erstellung des physikalischen Modells wurden zunächst die Geometrien mit den Massen und Trägheiten der einzelnen Achsen abgebildet (gelbe Blöcke in Abb. 2), welche durch Antriebsmodule verbunden sind. Jedes Antriebsmodul enthält das Gelenk, das Getriebe und den Motor sowie die Reglerstruktur einer Achse des Roboters.
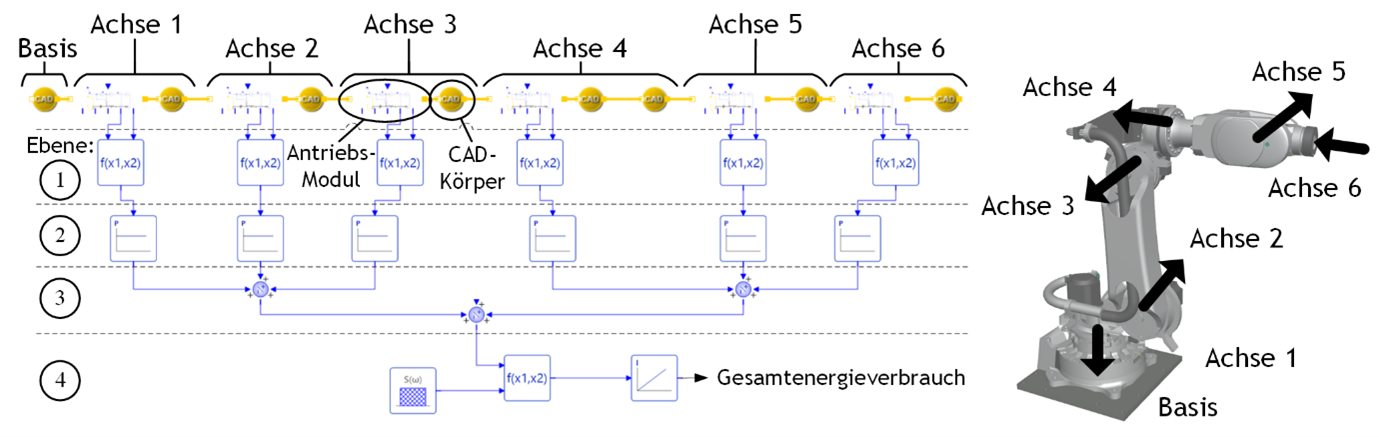
Aus den mechanischen Größen Drehmoment und Drehzahl der jeweiligen Achse wird in Ebene 1 (vgl. Abb. 2) eine Leistung berechnet. Über den Wirkungsgrad erfolgt die Umrechnung in die elektrische Leistung (Ebene 2). Nach Summenbildung über alle Achsen in Ebene 3 folgt in Ebene 4 die Addition der durch die Peripherie verursachten Grundlast und die Integration der Gesamtleistung zu dem Energieverbrauch.
Abbildungsgenauigkeit durch Energieverbrauchsmessung realer Roboter
Um die Abbildungsgenauigkeit des Simulationsmodells einschätzen zu können, mussten die Berechnungsergebnisse mit Messdaten zu den realen Energieverbräuchen verglichen werden. Hierzu wurde eine Energieverbrauchsmessung am realen Roboter durchgeführt und die Messergebnisse mit den simulierten Ergebnissen für die gleiche Bewegungsvorgabe verglichen. Nach Kalibrierung bestimmter Modellparameter wie den Massenträgheiten und den Reglereinstellungen anhand der Messdaten, ist nur noch eine geringe Abweichung zwischen den gemessenen und simulierten Leistungs- und Energieverläufen zu erkennen (Abb. 3).
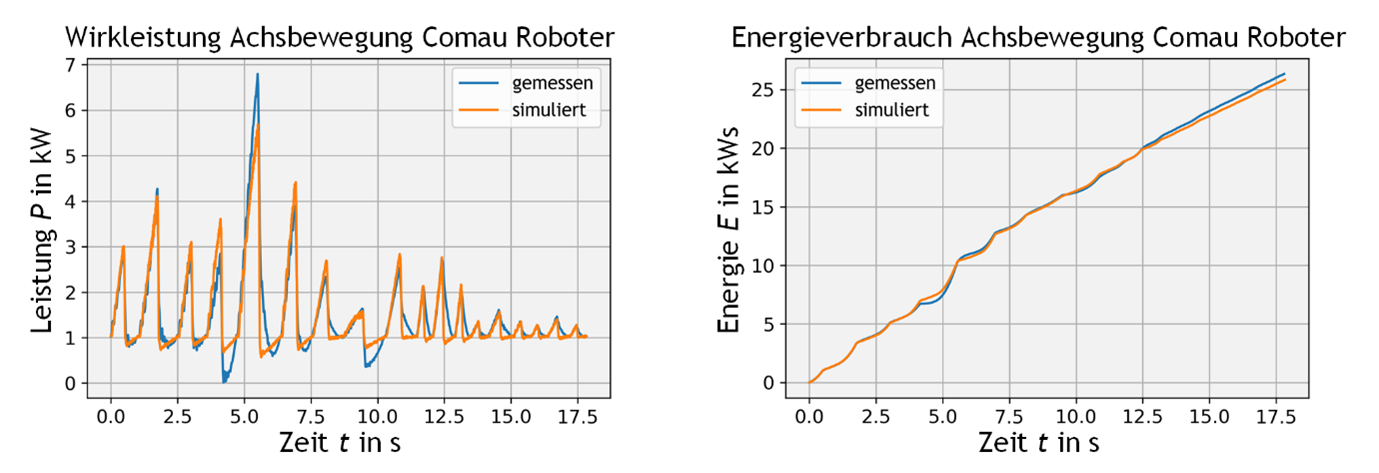
Diese können auf vereinfachende Annahmen bei der Modellbildung zurückgeführt werden. Der Fokus des Modells liegt hier jedoch auf der Vorhersage des Energieverbrauchs. Der relative Fehler dessen liegt fast immer unter 3 %. Insofern spiegelt das Modell für diese Bewegung den Energieverbrauch sehr genau wider.
Um den Energieverbrauch für jede beliebige Bewegung auf Grundlage des Steuerungscodes bewerten zu können, erfolgt auf Anlagenebene (Abb. 1) die Integration des physikalischen Modells in eine Umgebung zur virtuellen Inbetriebnahme (VIBN). Dort wird das Modell unseres Anwendungsfalls mit einer virtuellen Steuerung (Software-in-the-Loop Simulation) verbunden. Außerdem wird es über die FMI-Schnittstelle um die Energieverbrauchsberechnung erweitert. Für spezifische Roboterbewegungen wie Handlingprozesse oder Montageaufgaben kann so hochaufgelöst der Energieverbrauch simulativ auf der Basis realer Steuerungsvorgaben bestimmt werden (Abb. 4). Der Modellabgleich für den SiL-Aufbau ist Gegenstand aktueller Untersuchungen.
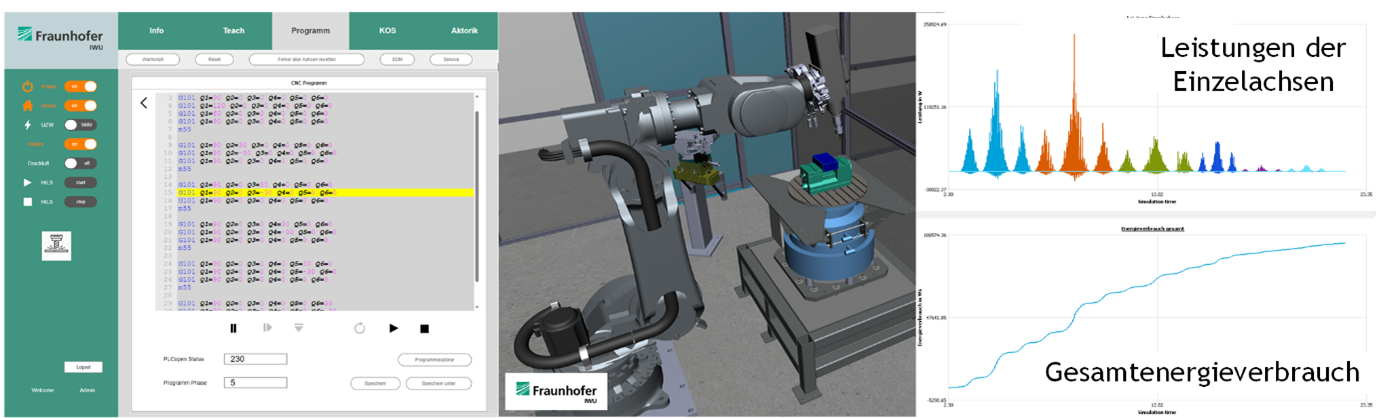
Fazit & Kontakt
Zusammenfassend lässt sich feststellen, dass der Energieverbrauch des Roboters in unserem Anwendungsfall mit einer hinreichenden Genauigkeit (Abweichung zu real gemessenem Verbrauch <5 %) simulativ vorhergesagt werden kann. Auf dieser Methode aufbauend können beispielsweise Prozessbewertungen vorgenommen oder nach Modellierung weiterer Maschinen und Anlagen energetische Optimierungen im Produktionsumfeld realisiert werden.
Sehen Sie einen Anwendungsfall für die Energieverbrauchssimulation in Ihrer Firma oder haben Sie Fragen zu diesem Thema, nehmen Sie gern Kontakt zu mir auf: leon.hollas@iwu.fraunhofer.de.
Headerbild: © Fraunhofer IWU