Agilität und Effizienz: Herausforderungen für die Produktionstechnik
Agile Produktionsstrukturen, hohe Qualitätsanforderungen und Energieeffizienz – Herausforderungen, denen sich erfolgreich produzierende Unternehmen stellen müssen. Grenzen, die durch die jeweils bestehende Maschinentechnik gesetzt werden, sind dabei besonders schwer zu überwinden. „Flexibilität und Transparenz in der Anlagentechnik ist daher aktuell besonders nachgefragt.“ berichtet Martin Laube (Director Engineering and Support bei Borsch Rexroth). „Die Antriebstechnik spielt bei Produktionsanlagen eine wichtige Rolle wenn es darum geht, zukunftssicher zu produzieren – ganz gleich, welche Maschine man vor sich hat.“ Insbesondere dann, wenn hohe Energie- und Kraftdichte benötigt werden, kommen bevorzugt Hydrauliklösungen zum Einsatz.
„Hydraulische Antriebe in der Pressentechnik sind daher nicht wegzudenken – im Gegenteil: die flexiblen Nutzungsmöglichkeiten und das große Potential zur Sensorierung dieser Systeme verspricht auch künftig eine stabile Rolle dieser Technologie in der Umformtechnik“ ist sich Hendrik Rentzsch, Abteilungsleiter am Fraunhofer IWU in Chemnitz, sicher. „Eine Schlüsselrolle nimmt dabei die Vernetzung der Systembestandteile untereinander, die Dezentralisierung der Steuerungshierarchien in Kombination mit dem Einsatz intelligenter Komponenten und Sensoren ein. Somit ist es möglich, zugleich die Potentiale transparenter Produktion und effizienter Betriebsstrategien der hydraulischen Anlagen zu nutzen.“
Komplexität wird beherrschbar
Ein besonders hoher Nutzen kann erreicht werden, wenn nicht in abgeschlossenen Baugruppen gedacht wird, sondern das Produktionssystem als Ganzes bei der Beurteilung und Auswertung von Sensordaten zugrunde liegt. Wie dies gelingen kann und welche Benefits entstehen, haben Bosch Rexroth und das Fraunhofer IWU In einem gemeinsamen Innovationsprojekt gezeigt. Dabei ist ein Demonstrator entstanden, der diese Potentiale erlebbar macht.
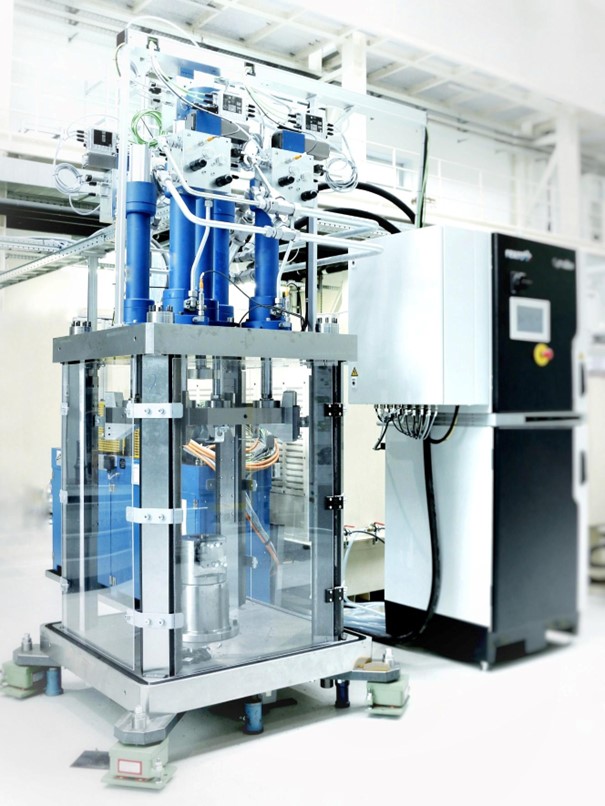
Die Basis bildet dabei ein komplexer Fließpressprozess, wie er in Großserie genutzt wird, um beispielsweise Antriebskomponenten mit größter Präzision herzustellen. Martin Laube, sagt: „Wir wollen zeigen, welche positiven Effekte die Zusammenführung unserer smarten Produkte bzgl. Aggregat (CytroBox) und Aktorik mit sich bringen kann. Dabei geht es uns nicht nur um die Möglichkeit, Produktionsprozesse und resultierende Qualitätskenngrößen inline zu überwachen.”
Quelle: © Fraunhofer IWU
Auch die signifikante Einsparung von Energie für den Betrieb derartiger Anlagen bei einem Einsatz moderner hydraulischer Konzepte kann an diesem Demonstrator gezeigt werden.“, so Martin Laube. Somit kann der Product Carbon Footprint (PCF) nicht nur transparent dargestellt, sondern künftig auch deutlich reduziert werden.
Die konsequente Vernetzung der Einzelsysteme untereinander in Kombination mit der Maschinensteuerung macht jedoch noch mehr möglich. „Die konsistent vorliegenden Datensätze aus Maschine und Hydrauliksystem sind prädestiniert für den Aufbau und die Nutzung eines digitalen Systemzwillings. Somit lässt sich datenbasiert auch eine Vorausschau für die Produktionsqualität, den Energieverbrauch oder den Systemzustand realisieren.“ stellt Hendrik Rentzsch fest und gibt damit einen Ausblick für künftige gemeinsame Entwicklungsschritte.
Headerbild: © Fraunhofer IWU