Das Spannen von Schmiedegesenken ist komplex
Das Rüsten von Schmiedewerkzeugen stellt einen komplexen Prozess dar, der aufgrund der spezifischen Produktions- und Randbedingungen des Hammers zahlreiche Iterationen erfordert. Eine wesentliche Ursache dafür ist die hohe Anforderung an die Robustheit der Systeme. Automatisierungslösungen oder Spannsysteme, welche aus einer Vielzahl von Einzelteilen aufgebaut sind, können für große Schmiedehämmer kaum eingesetzt werden, da das Risiko des Ausfalls dieser Systeme durch Beschädigungen beim Spannen oder im Schmiedeprozess unverhältnismäßig hoch ist. Oftmals bleibt der Einsatz von Schlagkeilsystemen mit Beilagen die einzige Alternative, um große Gesenke sicher im Ober- und Unterbär zu fixieren. Entsprechend erfolgt der Spannprozess mit äußerst robusten und teilweise simplen Werkzeugen: Die Schlagkeile werden durch den Einsatz von mechanischen, hydraulischen oder pneumatischen Keilrammen positioniert. Eine exakte Beaufschlagung der Gesenke mit Spannkraft ist damit kaum möglich. Das hat zur Folge, dass die Qualität des Spannprozesses stark von der Fachexpertise der Werker abhängt.
Mangelnde Reproduzierbarkeit und Spannprozesse, bei denen die Spannmittel oder sogar das Gesenk beschädigt werden, sind keine Seltenheit – das soll sich künftig ändern. Am Fraunhofer IWU wurde daher im Forschungsprojekt „sGs – Sensitives Gesenkspannsystem“ die Spannsituation von Schmiedegesenken in Hämmern simulativ und experimentell analysiert. Die Durchführung solcher Untersuchungen, die in der Literatur bislang kaum zu finden sind, stellt einen bedeutenden Beitrag dar. Das gilt insbesondere in den rauen Umgebungs- und Prozessbedingungen im Schmiedeumfeld, die die messtechnischen Möglichkeiten stark limitieren.
Ein Blick in die Spannstelle
Für eine umfassende Analyse der Spannsituation, Spannkraftänderungen und Einflussgrößen wurden im Forschungsprojekt umfangreiche simulative und experimentelle Untersuchungen durchgeführt. Dazu konnte ein Messkonzept entwickelt und systemisch realisiert werden. Mit diesem Messsystem ist es möglich, die Spannkraft, deren Verteilung, Spannkraftänderungen, Beschleunigungen und Temperaturen während des Spannprozesses sowie während des Schmiedeprozesses zu messen. Das resultierende Messsystem im Einsatz ist in Abbildung 1 dargestellt.
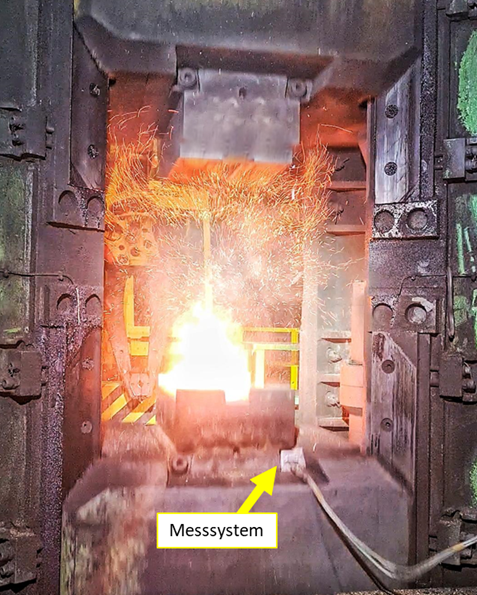
In den Messungen wurde bestätigt, was FEM-Simulationen gezeigt haben: Die Reaktionskraftverteilung an den Spannflächen zwischen Gesenk und Bär ist sehr heterogen und stark von den wirkenden Belastungen am Gesenk abhängig (vgl. Abbildung 2).
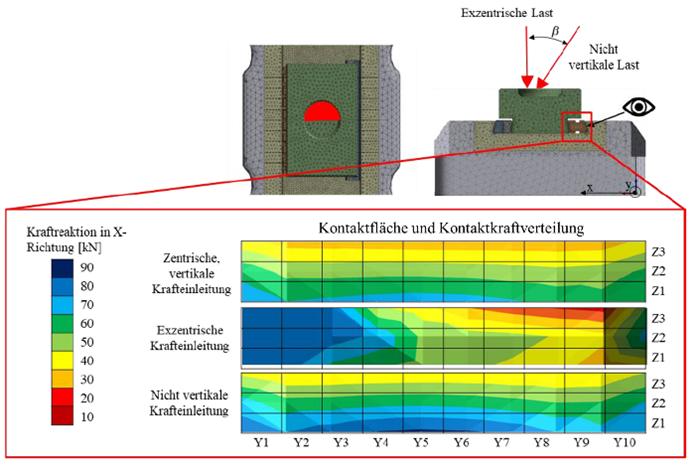
Ein Resultat dieser starken lokalen Belastungen sind immense Verschleißerscheinungen an den Spannflächen aller beteiligter Komponenten. Fresserscheinungen und Oberflächenzerrüttung bis hin zu plastischer Deformation wurde bei den experimentellen Analysen bereits nach wenigen Spannprozessen und Hammerschägen beobachtet. Die Folgeeinflüsse diverser Effekte und anderer Einflussparameter auf den Spannprozess konnten im Laufe des Projektes analysiert und klassifiziert werden. Als Bewertungsbasis wurden fünf spannprozessbeschreibende Kennwerte identifiziert, für welche eine Einflussanalyse durchgeführt wurde:
- Spannkraft
- Spannkraftverteilung
- Spannkonsistenz
- Reproduzierbarkeit
- Positionierungsqualität
Die Ergebnisse dieser Einflussanalyse sind in Abbildung 3 dargestellt. Dabei kann festgehalten werden, dass insbesondere die geometrischen Einflussparameter Bär- und Gesenkwinkel sowie Änderungen in den Beilagen und der Konaktierung (bspw. durch die oben beschriebenen Effekte) den Spannprozess immens beeinflussen. Hinzukommend ist die Methode, wie die notwendige Spannkraft aufgebracht wird, entscheidend für einen gelingenden Spannprozess.
Automatisierung und Robustheit: Neues Spannkonzept
Anhand der experimentellen und simulativen Untersuchungen konnte abschließend innerhalb des Projektes ein Konzept für eine neue Spannmethode erarbeitet werden. Dabei wurden den beiden wesentlichen Anforderungen (Automatisierung und Robustheit) dadurch Rechnung getragen, dass ein modularer Aufbau die temporäre Kopplung einer spannkraftaufbringenden Einheit mit einem monolithisch ausgeführten Spannkeilsystem ermöglicht. Somit kann der Spannprozess automatisiert erfolgen und die Spannkomponenten sind dennoch bestmöglich vor Beschädigungen geschützt.
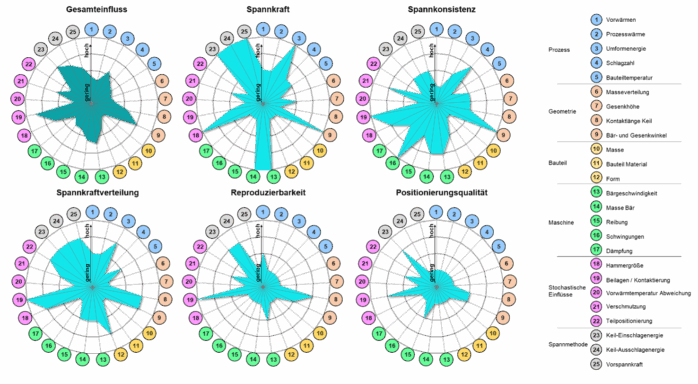
Sollten Sie Fragen oder Anmerkungen haben, freuen wir uns über eine Kontaktaufnahme unter: robin.kurth@iwu.fraunhofer.de.