Welche Herausforderungen existieren aktuell für die Zulieferindustrie der Luft- und Raumfahrt?
Die Bedeutung der Zulieferindustrie in Deutschland, besonders in der Luft- und Raumfahrt, ist in den vergangenen Jahren stetig gestiegen. Daher werden Betriebe aus dieser Zulieferindustrie, welche sehr stark durch KMU’s geprägt ist, auch hidden champions genannt. Charakteristisch für die Zulieferindustrie, sind eine hohe Fertigungstiefe, Anzahl an Produktvarianten und die wechselnden Produktanforderungen durch die zunehmende Individualisierung der Luftfahrzeuge und zugehörigen Einzelkomponenten. Neue Innovationen für die Zulieferer der Luft- und Raumfahrtindustrie werden aktuell mit der informationstechnischen Vernetzung aller an der Herstellung beteiligten Instanzen (Menschen, Werkstücke, Maschinen) erwartet. Auf diesem Weg profitieren KMU-Zulieferer, die aus ihren Anforderungen abgeleitete, firmenspezifische Lösungen schrittweise realisieren und sich somit gegenüber der Konkurrenz abheben.
Ein erfolgsversprechender Ansatz für ein Fertigungsunternehmen liegt in der Akquise vorhandener Daten aus bestehenden Einzelprozessen bzw. Prozessketten und die anschließende intelligente Auswertung zur Erlangung neuen Wissens. Eine Schlüsselrolle nehmen digitale Prozess-Zwillinge ein. Mit ihnen lassen sich beispielsweise die Qualität der Fertigungsprozesse und Produkte dokumentieren, bewerten und beeinflussen. Große wirtschaftliche Reserven finden sich in der Zerspanung komplizierter Geometrien (5-Achs Fräsapplikationen) bei gleichzeitig hohem Zeitspanungsvolumen. Besonders in der Luft- und Raumfahrtindustrie müssen sicherheitsrelevante Bauteile aus dem “Vollen”, d.h. aus einem Materialblock herausgearbeitet werden. Der Anteil des zu zerspanenden Materialvolumens kann hierbei bis zu 90% betragen. Diese Bearbeitungsschritte sind sehr zeit- und kostenaufwendig, insbesondere bei schwer zerspanbaren Werkstoffen. Daher sind neue Ansätze erforderlich, diese Prozesse effektiver auszulegen und dabei die Qualitätsvorgaben einzuhalten. Das gilt insbesondere bei Bauteilen, die erstmalig gefertigt werden.
Wie lassen sich wirtschaftliche Reserven erschließen und dabei die Qualität erhöhen bzw. den Ausschuss reduzieren?
Kern des neuen Lösungsansatzes sind digitale Prozess-Zwillinge, die für jedes zerspante Bauteil erzeugt werden und den jeweiligen bauteilindividuellen Fertigungsprozess mit all seinen Charakteristika virtuell abbilden. Diese digitalen Prozess-Zwillinge beruhen auf den Planung- und Prozessdaten, die während der Zerspanprozesses akquiriert werden. Zur automatisierten Erzeugung dieser Zwillinge werden alle an der Fertigung bzw. in der Fertigungsumgebung beteiligten Daten- und Informationsquellen verknüpft und zusammengeführt. Dadurch wird ein wesentlicher Schritt zur kompletten Digitalisierung der Fertigungskette realisiert. Die hochfrequente Erfassung der Prozessdaten erfolgt über Edge-Devices, die mit der Steuerung der Werkzeugmaschine verknüpft sind. Dabei werden alle geometrischen, kinematischen und leistungsspezifischen Daten während des Bearbeitungsprozesses akquiriert und durch intelligente Datenverarbeitungsmethoden auf Basis eines neuen Informations- und semantischen Datenmodells synchronisiert, strukturiert und aufbereitet.
Diese Prozessdaten werden mit den Werkzeug-, Maschinen-, Technologie- und Werkstückdaten verknüpft und auf Basis eines Informationsmodells zusammengeführt. Darauf aufbauend werden automatisiert zerspanungsrelevante technologische Modelle zur Bestimmung notwendiger Prozess- und Qualitätskenngrößen implementiert, um ortsdiskret die Prozesskenngrößen visuell darzustellen. Mit der durchgängigen digitalen Repräsentation aller Bearbeitungsschritte im digitalen Prozess-Zwilling werden Probleme während der Herstellung, d.h. Abweichungen von den Planungsvorgaben, direkt erkannt und es können zielgerichtet Maßnahmen zur Qualitätssicherung bzw. zur Optimierung des Bearbeitungsprozesses abgeleitet werden.
Was muss konkret umgesetzt werden, um die Herausforderungen zu meistern und die Potenziale zu nutzen?
Um den beschriebenen Lösungsansatz zu verwirklichen ist die Softwareentwicklung eines digitalen Assistenzsystems erforderlich, in welchem Prozess-Zwillinge von komplexen 5-Achsfräsapplikationen erzeugt und die Ergebnisse für Soll/-Ist Vergleiche genutzt werden können. Diese Vergleiche fördern das Verständnis für die Zusammenhänge im Prozess. Außerdem bilden sie die Grundlage für schnellere und zielgenauere Entscheidungen bzgl. erforderlicher Prozessanpassungen. Diese Anpassungen führen zu einer höheren Produktivität, wenn Leistungsreserven identifiziert und genutzt werden können. Außerdem werden die geforderten Qualitätsanforderungen an das komplexe Frästeil schneller einstellbar und Fehler eher identifizierbar.
Die Umsetzung dieses digitalen Assistenzsystems erfolgt in einem Forschungsverbund, in welchen die N+P Informationssysteme GmbH die Softwarearchitektur entwickelt und die Umsetzung der Software vorantreibt. Die PMG Precision Mechanics Group entwickelt und implementiert eine Datendrehscheibe im Unternehmen. Das Fraunhofer IWU entwickelt die entsprechenden Informations- und Prozessmodelle. Die Bündelung von Kompetenzen in Fertigungstechnologien, Unternehmensprozessen und Softwareentwicklung resultieren in Innovationen mit konkreten Effizienzgewinnen.
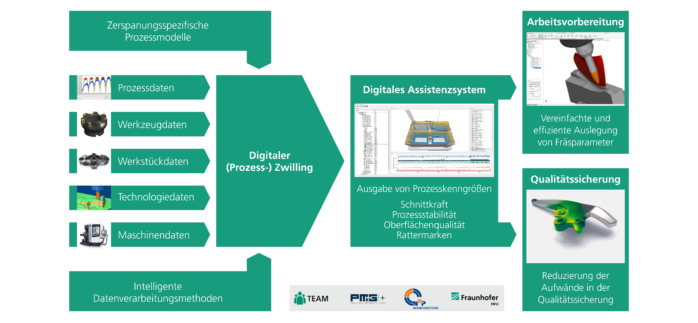
Titelbild: © Christian Hermeling/Albrecht Hänel (Fraunhofer IWU)
Grafik: © Albrecht Hänel
Kommentar hinzufügen