Freiheitsgrade im Betrieb nutzen
„Die Auswahl hydraulischer Pumpenantriebslösungen ist vielfältig. Es existieren Motor-Pumpenkombinationen, bei denen der technologisch erforderliche Volumenstrom entweder durch Variation der Motordrehzahl oder durch Anpassung der Fördermenge pro Pumpenumdrehung vorgegeben werden kann. Somit ist es möglich, die Antriebseinheit an die technologisch erforderlichen Leistungsparameter der Maschine anzupassen. Dies geschieht jedoch immer in Abhängigkeit vom Wirkungsgrad der Pumpen-Motor-Kombination, der von diesen Leistungsparametern bestimmt wird. Insbesondere im Teillastbereich der Antriebskombination existieren Betriebsparameter fernab des optimalen Wirkungsgrades. Das Antriebssystem garantiert die erforderlichen Prozessparameter, verbraucht aber dabei relativ viel Energie.“ erläutert Dr. Leonhard, Design Engineer R & D Business Unit Chemnitz Pump & Motor Division Europe bei Parker.
Eine Kombination der Verstellmöglichkeiten auf Pumpen- und Motorseite kann hier Abhilfe schaffen. „Statt einen einzigen Freiheitsgrad zur Erzeugung des erforderlichen Pumpenvolumenstroms kann man nun beide Stellgrößen (Motordrehzahl und Fördermenge der Pumpe pro Umdrehung) nutzen und aufeinander abstimmen. Dadurch ist es auch bei sich ändernden Anforderungen an den Leistungsbedarf möglich, die Motor-Pumpen-Einheit stets im optimalen Betriebspunkt zu betreiben.“ so Willy Reichert, wissenschaftlicher Mitarbeiter am Fraunhofer IWU in Chemnitz.

Bewehrte Technik wird kognitiv
Die Kombination beider Systeme – Verstellpumpe mit drehzahlgeregeltem Motor – ist nicht komplett neu. Die Herausforderung besteht darin, beide Einstellgrößen für einen optimalen Betrieb vorzugeben. „Was durch Auslegungsrechnung für einen Betriebsfall händisch funktionieren kann, ist für sich ändernde Betriebsbedingungen nicht trivial lösbar.“ stellt Willy Reichert klar. „Eine speziell entwickelte Software, die direkt auf die Controller-Unit des Antriebssystems installiert werden kann, übernimmt genau diese Aufgabe“. Die Software analysiert dabei den aktuellen Wirkungsgrad während des Betriebes, berechnet die optimalen Betriebsparameter und passt diese zyklisch an. Somit kann ohne Zutun des Bedieners ein optimaler Systembetrieb ermöglicht werden, der autark auf sich ändernde Randbedingungen reagiert. In Summe entsteht so ein kognitives System zur Integration in komplexe Anlagen.
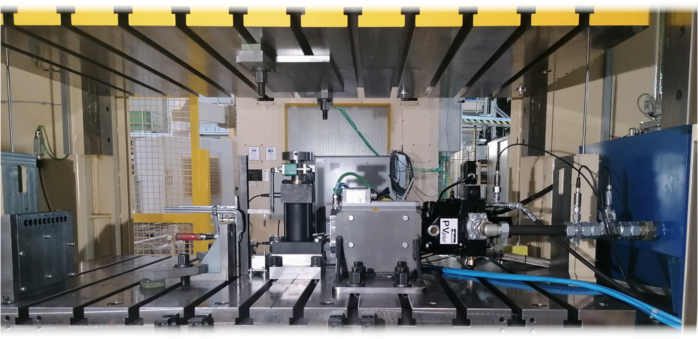
Systemverständnis – der Schlüssel für erfolgreiche Entwicklungen
„Wichtig bei der Entwicklung war insbesondere, dass die autarke Anpassung der Betriebsparameter an Pumpe und Motor nicht zu einer Änderung der Qualitätsparameter im Produktionsprozess führt – schließlich beeinflussen wir damit auch das hydro-mechanische Systemverhalten.“ ergänzt Dr. Leonhard. Um dies zu untersuchen, wurden am Fraunhofer IWU umfangreiche System-Simulationen und ein Versuchsstand aufgebaut, mit denen Szenarioanalysen durchgeführt wurden. Es zeigte sich, dass durch Hinzufügen geeigneter Randbedingungen die Robustheit der Software entsprechend beeinflusst werden kann, um die Prozessparameter sicherzustellen. Derzeit befindet sich das System in Felderprobung und soll ab 2024 als Produkt von Parker Hannifin GmbH ausgerollt werden.
Für Rückfragen und Anmerkungen steht Ihnen Herr Robin Kurth als Gruppenleiter “Umformmaschinen” gerne via LinkedIn oder unter folgender Mailadresse zur Verfügung: robin.kurth@iwu.fraunhofer.de.