Was in der Natur seit jeher gilt, trifft auch zunehmend auf Produktionsprozesse zu. Effizienz und Qualität sind traditionelle Maßstäbe industrieller Produktion. Aber erst seit einigen Jahren können Maschinen und Komponenten durch integrierte Sensoren und eingebettete Elektronik mit Intelligenz ausgerüstet und zur Adaptivität befähigt werden. Auf diese Weise wird die Effizienz und Qualität auf ein neues Level gehoben. Bei Zerspanprozessen spielt die Hauptspindel von Werkzeugmaschinen dabei eine zentrale Rolle, da sie in direktem Kontakt zum Bearbeitungsprozess steht und das Bearbeitungsergebnis direkt beeinflussen kann – gemeinsam mit der Werkzeugmaschine. Die Grundlage einer jeden Beeinflussung bildet jedoch die wirkstellennahe Erfassung von Prozesskräften und -zuständen.
Prozesskraftmessung durch die Werkzeugspindel als industrieller Entwicklungstrend
Das Ziel, Prozesskräfte in industriellen Anwendungen in Echtzeit zu messen, zu analysieren und schnell auf unerwünschte Abweichungen reagieren zu können, beschäftigt Hersteller und Anwender spanender Werkzeugmaschinen bereits seit einiger Zeit. Zuletzt wurden im Umfeld von Werkzeugmaschinen immer mehr Systeme vorgestellt, die, basierend auf verschiedenen physikalischen Prinzipien, Messungen im Bearbeitungsprozess ermöglichen. Neben Werkzeughalter-basierten Systemen zählen auch vermehrt spindelintegrierte Systeme dazu. Die Analyse der Sensordaten erfolgt bei bestehenden Systemen jedoch meist in Einheiten außerhalb der Spindel. Eine integrierte Lösung, welche die Spindel zu einem eigenständigen, intelligenten Subsystem in der Maschine macht, existiert bisher nicht. Das Fraunhofer IWU hat zusammen mit dem Spindelhersteller SN Spindeltechnik eine sensorischen Spindel bis zum Prototypen entwickelt, der auf Basis spindelintegrierter Kraftmesssensoren, Elektronik und Analysesoftware Überwachungs- und Regelungsparameter für die Spindel und die Prozesssteuerung der Maschine bereitstellt.
Bei der Entwicklung des Systems wurde darauf Wert gelegt, eine hohe Sensitivität bei der Kraftmessung zu erreichen und gleichzeitig die Steifigkeit der Spindel nicht zu reduzieren. Die Integration der Sensoren in die Spindelstruktur erlaubt die Verwendung handelsüblicher Werkzeughalter. Für eine Signalauswertung wurde eigens eine Transformationssoftware entwickelt, welche die verschiedenen Werkzeugparameter berücksichtigt und die gemessenen Kraftwerte von der Mess- zur Wirkstelle umrechnet. Durch die spindelintegrierte Analysesoftware wird die Transformation innerhalb der eingebetteten Elektronik ausgeführt. An diese können außerdem weitere, im Spindelbau etablierte Messsysteme wie Spannzustandsabfrage, Drehgeber, Drucksensoren usw. angebunden werden. Die Kommunikation mit der Maschine wird im Standardfall ausschließlich über das EtherCAT Protokoll realisiert. Für die Nachrüstung vorhandener Maschinen können benötigte analoge Signale auch über herkömmliche Schnittstellen ausgekoppelt werden.
Tests des Prototypen mit vielversprechenden Ergebnissen
Nachdem alle entwickelten Teilsysteme in den Prototypen integriert wurden, konnten Ende vergangenen Jahres erste Tests der Spindel auf einer Fräsmaschine des Fraunhofer IWU erfolgen. Zur Bewertung der Messergebnisse der Spindeltests wurden Referenzmessungen mittels Tischdynamometern und ein Data Logging von Antriebsgrößen der Maschine durchgeführt. In den Versuchen wurden mit einem zweischneidigen 20 mm Schaftfräser und einem 63 mm Messerkopf Nuten in Aluminium gefräst. Somit konnten die Einflüsse geometrisch unterschiedlicher Werkzeuge auf die Messergebnisse untersucht werden.
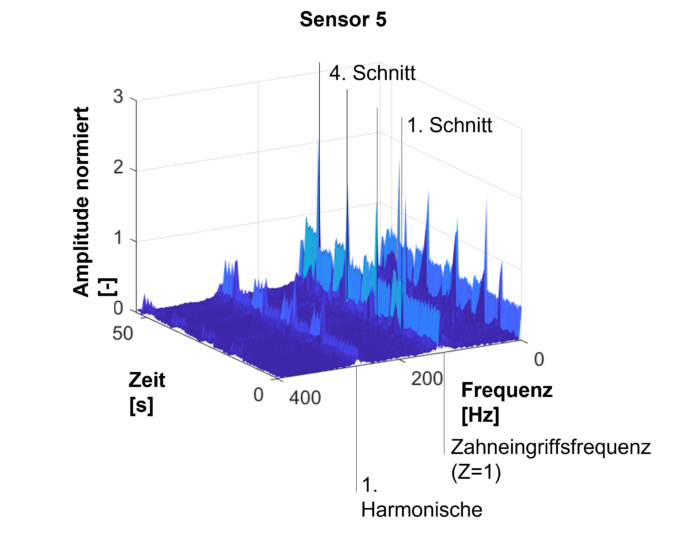
Die Abbildung zeigt die Fast-Fourier-Trasformation (FFT) des Signals eines integrierten Kraftsensors. In den Versuchen zum Proof-of-Konzept wurden die Amplituden normiert, da geeignete Kalibriermethoden noch entwickelt werden musste. Die vier durchgeführten Schnitte sowie die markanten Frequenzanteile sind darin jedoch gut erkennbar. Da in diesem Versuch mit einem einschneidigen Werkzeug gearbeitet wurde, fallen die Drehzahl und die Zahneingriffsfrequenz zusammen.
Die Versuche zeigten, dass das Gesamtsystem funktioniert und dass die integrierte Sensorik auch kleinste Parameteränderungen schnell erfassen kann. In den Signalanalysen konnten prägnante Frequenzanteile wie Drehzahl, harmonische Frequenzen bzw. Schneideneingriffe sicher detektiert werden. Auch Unregelmäßigkeiten und instabile Bearbeitungszustände, wie Rattern, konnten in den Signalen sicher erkannt werden. Die erfolgreiche Inbetriebnahme des Prototyps und der Funktionsnachweis des Gesamtsystems ist für die Projektpartner Grund zum Feiern. Aber auch, dass die Entwicklung noch nicht abgeschlossen ist und woran weitere Forschungs- und Entwicklungsarbeiten anknüpfen müssen, ist in den Versuchen deutlich geworden.
Herausforderungen müssen gelöst werden
Nun muss die intelligente Werkzeugspindel von ihrem Prototypenstatus in ein seriennahes Produkt überführt werden. Dafür werden eine betriebssichere Selbstkalibrierung des Systems sowie die Möglichkeit, werkzeugspezifische Kennwerte automatisch in die Auswerteelektronik zu übernehmen, vorgesehen. Zudem wird die interne Daten- und Verarbeitungsrate sowie Rechen- und Speicherkapazität weiter erhöht – bei gleichem Bauraum. Diese Applikationen und Leistungssteigerungen bilden die Grundlage für die zukünftige Implementierung von Algorithmen zur Auswertung weiterer Spindel- und Prozessparameter.
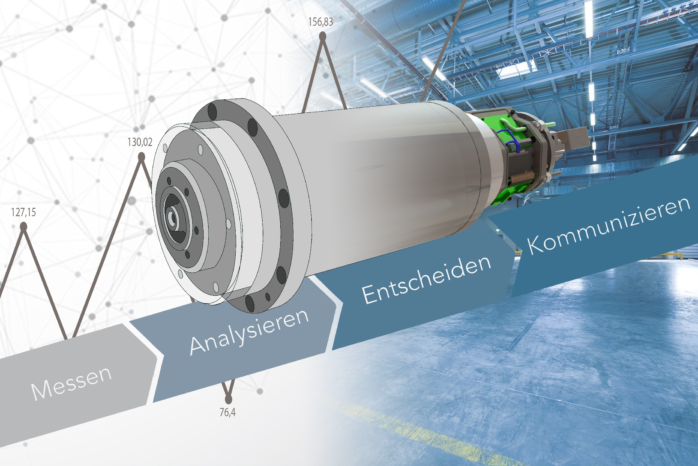
Fazit: Der erfolgreiche Test des ersten Prototyps zeigt, dass das Grundprinzip der intelligenten Werkzeugspindel funktioniert. Doch die Forschenden müssen sich weiteren spannenden Herausforderungen stellen: Neben der Optimierung der integrierten Elektronik spielen zukünftig vor allem die Implementierung weiterer Analyse-Algorithmen und die Steigerung der Robustheit und Leistungsfähigkeit des Systems eine wichtige Rolle.
Für Rückfragen steht Ihnen Herr Marian Noack sehr gerne unter folgender Mailadresse zu Verfügung: marian.noack@iwu.fraunhofer.de.
Headerbild: © Fraunhofer IWU